|
|
Sunday, 19 August 2007
|
|
I recently finished this bone carving. A simple, but stylized
version of hei Matau or fish-hook design. 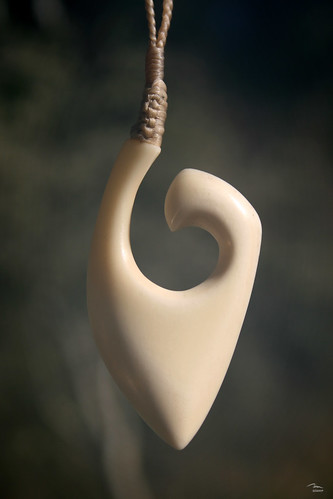
1:43:03 PM
|
|
|
Saturday, 4 August 2007
|
|
I've constructed this new piece of kite aerial photography equipment. I needed a line winder that could hold more line, and handle having the line wound on under pressure. Made from Tasmanian Backwood this winder is very solid and as you can see it holds 1000 feet of 250lb line no problem. If wound on tightly it could probably hold 2000 feet. The white decorative bits are beef bone inlays and the hook for securing the line (when you don't want it to pay out anymore) is also made of beef bone. The great advantage of a winder like this is it enables me to wind a kite down pretty quickly and easily. I just 'winch' it in hand over hand. The line goes on in a figure eight so there are not twists. Before I had to pull in the line with gloved hands and let it pile on the ground, then wind onto the halo reels once the kite was grounded. If the wind was strong the line could be hard to grip when pulling the kite down... not any more. 
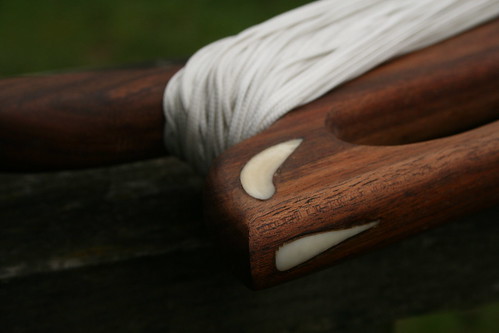
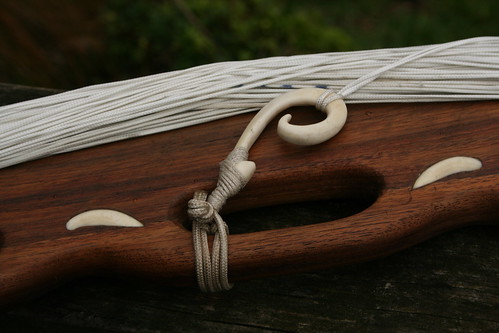
11:48:09 AM
|
|
|
Sunday, 1 July 2007
|
|
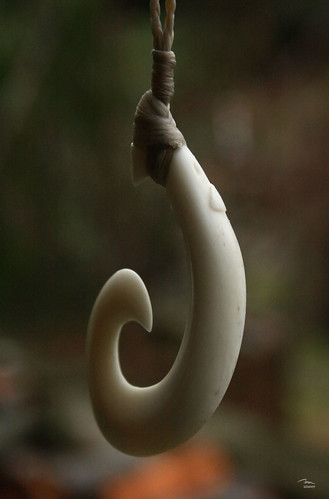
The winter months and rainy weekends have brought me back to bone carving. I finished this piece this weekend. It is the Hei Matau (fish hook) form but with this one I've tried to make it into a NZ freshwater eel (Tuna) shape. It has two fins and an eye on one side near the binding. It is carved from a rear shank beef bone.
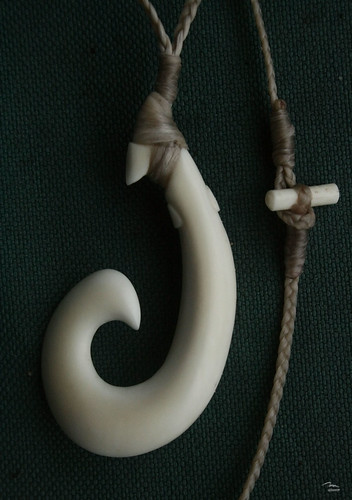
10:38:00 AM
|
|
|
Saturday, 2 June 2007
|
|
A couple of years ago I had a little go at bone carving to keep busy during the winter months. The pictures and text I posted then have since become pretty popular with google. I guess there isn't much info about bone carving on the web. I quite often get emails from people who are trying their hand at bone carving, just like I was, with questions about technique, materials, and tools. I'm no expert but I gladly pass on what I do know. This morning Con asked me about this lashing, the knotted ridge, seen here on my wahle tail carving: 
And here's how it's done: 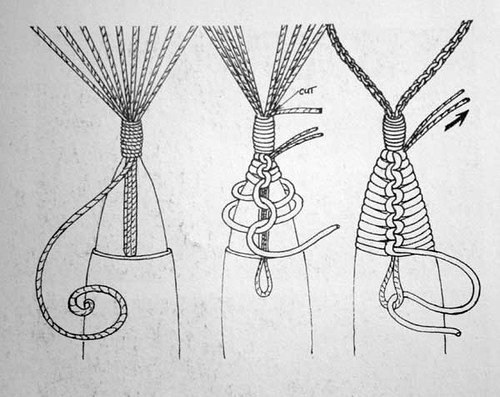
First a recess is carved into the bone for the lashing to sit into. This keeps it looking very tidy with the top surface of the lashing flush with the surface of the bone carving. A hole is drilled right through the peice at the base of the recess.The four lines of the main braid go through that hole, then up the back of the carving. (After the lashing is complete these are then braided to go around the wearers neck.) A seperate peice of cord is used for the lashing itself. Starting with a basic lashing at the top, the tail is then looped repeatedly around the back of the carving, and knotted through itself at the front. You keep looping and knotting until you cover the whole recess. the end is then pulled back under the lashing with a small loop left under the lashing for exactly that job. If you pull the tail end right up under the line of knots it makes them standout just that little bit more.I have used this lashing on several carving and it is very strong, and very stylish.
9:19:59 AM
|
|
|
Friday, 17 June 2005
|
|

6:35:53 PM
|
|
|
Saturday, 11 June 2005
|
|
 This little pendant was a test. I wanted to see what a not so perfect peice of bone would look like worked into a carving. The natural blemish on this peice is the slightly more porus bone where ligaments were once attached to the beef shank. I soaked the peice in blackcurrent juice to highlight the blemish. The more porus bone soaked up the colour of the juice, highlighting the grain.
I also wanted to try this whipping which will be a feature of the next peice I'm working on. Its a simple yet strong way to attached a cord to almost any shape leaving a nice line of knots down the front.

9:50:57 PM
|
|
|
Thursday, 2 June 2005
|
|
I finally found the beeswaxed nylon I have been looking for to finish off my bone carving with an authentic look. Being nylon its strong and not going to wear out in a hurry, and the beewax makes it look just like flax cord. The linen thread I tried, stretched and so the whipping needed redoing anyway. The beeswaxed nylon was easier to work with and I think it makes all the difference.

I finally found the stuff at a little place called The Bead Gallery. In an unassuming little house in the middle of and industrial area, surrounded by panel-beaters, battery wholesalers, and automotive workshops, is this Aladdin's cave full of everything to do with beads (and thats more than I imagined). If your in the area its worth a visit, especially if you're into making stuff.
6:53:09 PM
|
|
|
Sunday, 22 May 2005
|
|
My first bone carving project is finished. The material I wanted to use for the cord is still proving hard to find though. I wanted to use a bees-wax coated nylon, that is usually used for stitching leather, because it is very strong but also give the look of a traditional flax cord. I could go ahead and make it out of flax which would be very authentic but unfortunately no matter how well made flax cord will wear out eventually (and even faster through constant contact with the skin of the wearer). I have tried sewing shops, craft shops, hardware stores, etc but can't find the stuff I want anywhere. So in the photo below the braided cord and whipping is made from white linen thread which I have braided (with home made apparatus), and soaked in a cup of tea to give it a more natural looking colour. If I do manage to find some bees-wax coated nylon I will redo it, but for now the piece is finished.

10:42:23 AM
|
|
|
Saturday, 14 May 2005
|
|
After four days indoors with a head full of snot, I woke up this morning with the ability to breath through my nose again! The flu is all but gone, just in time for the weekend. Its one thing to mope around home feeling sick when you know you would only be at work otherwise, but on the weekend it drives me crazy!
My second bone carving is now underway. This one is shaped like a whale tooth which, once I get the shape just right, I will engrave. It's amazing how much polished beef bone looks like ivory. My first carving is now waiting for findings but the bee-wax coated nylon I want to use for braiding is proving difficult to source (I need to find a leather worker as apparently it's what they use). Rather than just drill a hole and use a slip-knot, I'm going use something like this. Being an ex-seaman, I appreciate a good whipping... wait, that didn't come out right...
9:17:13 AM
|
|
|
Thursday, 12 May 2005
|
|
I spent another day at home with the flu again today. At this rate I doubt if I'll get back to work this week. I worked on shaping my first bone carving project a little more. I can't really do much more now until I pick up some very fine sandpaper in town, but I'm pretty happy with it so far.

10:06:09 PM
|
|
|
© Copyright
2008
Murray Neill
. Last update:
5/10/2008; 2:46:06 p.m.
. |
|
October 2008 |
Sun |
Mon |
Tue |
Wed |
Thu |
Fri |
Sat |
|
|
|
1 |
2 |
3 |
4 |
5 |
6 |
7 |
8 |
9 |
10 |
11 |
12 |
13 |
14 |
15 |
16 |
17 |
18 |
19 |
20 |
21 |
22 |
23 |
24 |
25 |
26 |
27 |
28 |
29 |
30 |
31 |
|
Aug Nov |
|
|